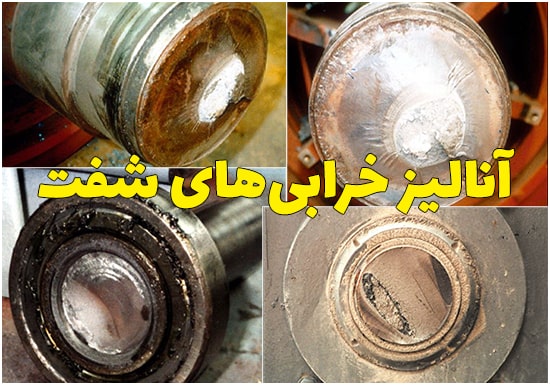
۰ تا ۱۰۰ آنالیز خرابیهای شفت (Shaft)
در ابتدا اشاره شود
که این مقاله ترجمه شده بخشی از کتاب Root Cause Failure Analysis ویرایش
دوم میباشد. اکثر خرابیهای شفت به دلیل ترکیبی از تنشهای مختلف است که
بر مجموعه روتور اعمال میشود. تا زمانی که تنشها در محدوده طراحی و
کاربرد مورد نظر حفظ شوند، خرابی شفت نباید در طول عمر مورد انتظار موتور
رخ دهد. این تنشها را میتوان به گروههای زیر تقسیم کرد:
۱) دینامیک/مکانیکی (Dynamic/Mechanical)؛ اضافه بارها از جمله بارهای شوک ناگهانی، بارهای چرخهای (خستگی)، بار اضافه و خمش، بار پیچشی و بار محوری.
۲) محیطی (Environmental)؛ خوردگی، رطوبت، فرسایش، سایش و کاویتاسیون.
۳) حرارتی (Thermal)؛ گرادیانهای دما و خم شدن روتور در اثر حرارت (Rotor Bowing).
۴) باقیمانده (Residual)؛ فرآیندهای تولید و فرآیندهای تعمیر.
۵) الکترومغناطیسی (Electromagnetic)؛ بارگذاری جانبی و بسته شدن مجدد خارج از فاز.
در ادامه این مقاله هر ۵ گروه، نام برده شده مورد بررسی قرار میگیرد اما قبل از آن مروری بر مفاهیم اصلی در بحث آنالیز خرابیهای شفت داشته باشیم.
شکل زیر انواع محورهای روتور مورد استفاده در موتورهای الکتریکی را نشان میدهد.
بررسی جنس شفت موتور و شکل آنها
برای اکثر کاربردهای موتور، فولاد کربنی نورد گرم انتخاب خوبی است. هنگامی که بارهای بیشتری وجود دارد، فولاد آلیاژی
مانند کروم-مولیبدن (Cr-Mo) اغلب استفاده میشود. برای کاربردهایی که
دارای خوردگی شدید یا محیط تهاجمی (Hostile Environment) هستند، فولادهای
زنگ نزن مورد نیاز است. لازم به ذکر است که با انتخاب فولاد زنگ نزن، استحکام تسلیم و استحکام کششی را به نفع مقاومت در برابر خوردگی کنار گذاشته میشود.
در شکل زیر برخی از رایجترین جنس فولادهای شفت با نامگذاری AISI فولاد برای ساخت شفت را نشان میدهد.
بررسی منحنی تنش-کرنش
برای درک مکانیسم شکست یک شفت فولادی موتور، مهم است که رابطه بین تنش و کرنش برای جنس شفت همراه خواص مکانیکی آن مشخص شود. شکل زیر نمودار معمول تنش-کرنش برای یک فولاد شفت را نشان میدهد.
این
نمودار تنش-کرنش برای فولاد کربنی 0.18% نورد سرد شده را نشان میدهد تنش
تسلیم این فولاد 73,000 پوند در اینچ مربع (PSI) که تقریباً معادل 503 مگا
پاسکال (MPa) است. به عبارت دیگر تا تنش تسلیم، تغییر شکل در قطعه موقت یا
الاستیک است و پس از آن با تجاوز تنش از حد تنش تسلیم پیوند بین مولکولهای
فولاد تغییر کرده است یا پیوند مولکولی پاره شده (Torn Apart) و
نمیتوانند بازگردند در نتیجه قطعه دچار تغییر شکل دائمی یا پلاستیک خواهد
شد. در صورت ادامه روند افزایش تنش قطعه دچار از هم کسیختگی خواهد شد.
بررسی تنشهای اعمال شده بر شفتها
تنشهای اعمال شده بر شفتها به سه گروه زیر تقسیم میشوند.
۱- تنشهای برشی ناشی از انتقال گشتاور (یعنی در اثر بار پیچشی).
۲- تنشهای خمشی (کششی یا فشاری) ناشی از نیروهای وارد بر اجزاء ماشین مانند: چرخ دنده، پولی و غیره و همچنین به دلیل وزن خود شفت.
۳- تنشهای ناشی از بارهای پیچشی و خمشی ترکیبی.
قبل
از اینکه علل شکست شفت به طور دقیق تعیین شوند، ضروری است که بارگذاری و
تنشهای موجود در شفت را به وضوح درک کنیم. این تنشها بهترینگونه با
استفاده از نمودارهای آزاد (Free Body Diagrams) توضیح داده میشوند.
نمودار آزاد به سادگی یک طرح است که نوع و جهت نیروهای موجود بر روی یک
شفت تحت تنش کششی، فشاری و برشی را نشان میدهد. در آینده مقالهایی با
موضوع طراحی شفت منتشر خواهد شد که بحث تحلیل تنش اعمالی به شفت در آنجا
مورد بررسی قرار خواهد گرفت.
ابزارهای تجزیه و تحلیل شکست شفت
توانایی
توصیف دقیق میکرو ساختار و توپولوژی سطح یک شفت که دچار شکست شده است در
تجزیه و تحلیل شکست بسیار مهم هستند. ابزارهای رایجی که برای این کار در
دسترس هستند میتوانند به شرح زیر دستهبندی شوند:
چشمی (Visual)
میکروسکوپ نوری (Optical microscope)
میکروسکوپ الکترونی اسکن (Scanning electron microscope)
میکروسکوپ الکترونی تراگذر (Transmission electron microscope)
آنالیز متالورژیکی (Metallurgical analysis)
فرض
میشود که احتمالاً لازم باشد از خدمات یک آزمایشگاه متالورژی با تجربه
برای به دست آوردن بخشی از اطلاعات مورد نیاز استفاده شود. با این حال،
تعداد قابل توجهی از شکستها با داشتن دانش اساسی در مورد آنالیز خرابیهای
شفت موتور و بازرسی بصری قابل تشخیص هستند. سپس ممکن است از طریق یک
آزمایشگاه متالورژیک تأیید شوند. مطالب ارائه شده در این مقاله به بررسی
دقیق علت اصلی شکست کمک خواهد کرد.
علل خرابی شفتها
مطالعاتی برای تعیین کمیت علل خرابی شفت انجام شده است. یک مطالعه صنعتی برای ماشین آلات دوار نتایج زیر را نشان میدهد. این اطلاعات از کتاب Metallurgical Failure Analysis انتشارات McGraw-Hill نشر 1993ارائه شده است.
مطالعات غیر رسمی دیگری وجود دارد که نشان میدهد اکثر خرابیهای شفت موتور در محدوده 80 تا 90 درصد به پدیده خستگی مربوط میشود. زمانی که پدیده خوردگی و افزایش تنش به شرایط خستگی تحمیل میشود، این عدد به محدوده 90 درصد میرسد. از این رو، تمرکز اصلی این بخش، شکستهای مرتبط با خستگی خواهد بود.
تعریف فرآیند خستگی
خرابی
ناشی از خستگی در تنشهای چرخهای مکرر رخ میدهد، که میتواند کمتر از
استحکام تسلیم ماده شفت باشد. خستگی، با جوانه زنی ترک شروع میشود و با
پیشرفت ترکهای خستگی سطح مقطع مؤثر شفت را کم میکند تا جایی که شفت دیگر
تحمل بارهای اعمالی را نداشته باشد. در سطح مقطع شکست ناشی از خستگی
علائمی دیده میشود که به عنوان علائم ساحلی (Beach Marks) شناخته میشود،
زیرا شبیه علائمی هستند که امواج در ساحل از خود به جای میگذارند.
خرابی
ناشی از خستگی شامل موارد زیر است: اول، خستگی منجر به ترک اولیه در سطح
قطعه میشود. ثانیاً، ترک یا ترکها تا زمانی گسترش مییابند که سطح مقطع
محور باقیمانده برای تحمل بار بسیار ضعیف شود. در نهایت، شکستگی ناگهانی
در ناحیه باقی مانده رخ میدهد.
خرابی ناشی از خستگی معمولاً از نظریه
ضعیفترین محل پیروی میکنند. یعنی ترکها در نقطه حداکثر تنش یا حداقل
مقاومت ایجاد میشوند. این محل معمولاً در یک ناپیوستگی شفت جایی مانند جای
خار شفت است. متغیرهای زیادی وجود دارد که بر عمر خستگی یک شفت تأثیر
میگذارد. اینها شامل دما، محیط، تنشهای پسماند و نا همواریهای سطح میشود.
نمودارهای تنش چرخه (S-N)
از آنجایی که بیشتر خرابیهای شفت مربوط به خستگی است، نمودارهای تنش چرخه (S-N) یکی از راههای تعیین استحکام و محدودیتهای ناشی از اعمال بار سیکلی میباشد. نمودار حداکثر تنش در برابر تعداد چرخههای قبل از شکست، نمودار تنش چرخه یا معمولاً نمودار S-N نامیده میشود.
در شکل زیر نمودار (S-N) برای فولاد 1040 نشان داده شده است. برای فولاد، این نمودارها پس از تعداد چرخه مشخصی افقی میشوند. به عبارت دیگر مهم نیست چند چرخهی تنش در یک سطح تنش معین به قطعه اعمال میشود، در آن سطح تنش قطعه دچار شکست نخواهد شد. این سطح تنش که به صورت خط افقی مطابق شکل نشان داده شده است به عنوان حد خستگی یا استقامت (Fatigue or Endurance Limit) شناخته میشود.
ظاهر خرابی ناشی از خستگی
شکل ظاهر خرابی ناشی از خستگی تحت تأثیر انواع مختلف ترکها (Cracks)، علائم ساحلی (Ceach Marks)، علائم شعاعی (Radial Marks)، علائم شورون -وی شکل- (Chevron Marks)، نوک برشی (Shear Tip) و مجموعهای از توپولوژیهای دیگر است.
سطح شکستگی ناشی از خستگی معمولاً دو ناحیه مجزا را همانطور که در شکل زیر نشان داده شده است نشان میدهد. منطقه A شامل نقطه مبدا خرابی است و بسته به چرخههای بارگذاری و شروع و البته بار با سرعت نسبی کند گسترش مییابد. منطقه B ناحیه رشد آنی یا سریع است و تغییر شکل پلاستیکی بسیار کمی را نشان میدهد. در این شکل، هر دو منطقه رشد کند و مناطق آنی را میتوان مشاهده کرد. این شفت از قسمت شیار که سبب تمرکز تنش شده است شکسته است. به وجود علائم زبانه دار (Ratchet marks) در حاشیه شفت توجه کنید. اینها به منشأء ترکها اشاره میکنند. ترکهای منفرد به سمت داخل رشد میکنند و در نهایت در یک صفحه به هم میپیوندند.
یکی از محلهای شروع ترک خستگی در شفت محل جای خار (Keyways) است، ایجاد جای خار برای اطمینان از استقرار بدون لغزش پولی، چرخدنده و غیره الزامی است. این محل که سبب تمرکز تنش میشود به طوری که بسیاری از خرابی ناشی از خستگی در شفت از این محل آغاز میشوند.
تحلیل سطح مقطع ناشی از خستگی در شفت
علائم ساحلی (Beach Marks) موقعیتهای متوالی جبهه ترک را نشان میدهد. این علائم معمولاً در نزدیکی شروع ترک بافت صاف دارند و با رشد ترک زبرتر میشوند. (شکل 1)
علائم زبانه دار (Ratchet Marks) نشانه گویای چندین ترک منفرد هستند که در نهایت با هم ادغام میشوند و یک ترک را تشکیل میدهند. علائم زبانه دار در بین محلهای منشأء ترک دیده میشوند. (شکل 2)
علائم شورون -وی شکل- (Chevron Marks)، به منشأ ترک اشاره میکنند. برخی از خرابیها (مانند موردی که در زیر نشان داده شده است) دارای شورونهای بارزتری هستند. هر چه شکستگی شکنندهتر باشد، نقطه پایان شکست کوچکتر است. (شکل 3)
خرابیهای خستگی خمشی دورانی (Rotational Bending Fatigue Failures) زمانی رخ میدهد که هر قسمت از محور تحت بار تحت فشار و کشش متناوب قرار میگیرد. یک ترک میتواند در هر نقطهای از سطح که سبب تمرکز تنش شده است شروع شود و ممکن است به دلیل چرخش به طور ناهموار رشد کند. این شفت خاص دارای چندین نقطه شروع است که توسط علائم زبانه دار (Ratchet Marks) روی محیط نشان داده شده است. (شکل 4)
خرابیهای پیچشی (Torsional Failures) با ظاهر پیچ خورده (Twisted) روی شفت مشخص میشوند، اما بسته به میزان بار پیچشی و شکلپذیر یا شکننده بودن مواد، شکست ممکن است متفاوت ظاهر شود. این محور خاص قبل از شکست مقداری پیچ خوردگی را نشان میدهد. جوشکاری زائدهها (Spiders) بر روی شفت نقاط تمرکز تنش بودهاند. اگر مواد شفت انعطافپذیر باشد، قبل از شکست پیچش بیشتری نشان میدهد. اگر محور شکنندهتر باشد یا در معرض پیچش شدید باشد، شکستگی ظاهر خشنتری خواهد داشت. (شکل 5)
گروه بندی تنشهای اعمالی به شفت
۱) تنشهای دینامیکی و مکانیکی
تنشهای دینامیکی و مکانیکی (Dynamic and Mechanical Stresses)، در اثر حرکت شفت به آن وارد میشوند و شامل موارد زیر هستند:
الف) اضافه بارها، از جمله بارهای شوک ناگهانی (Overloads including sudden shock loads)
ب) بارهای چرخهای یا خستگی (Cyclic loads)
ج) بارهای چرخشی خمشی (Overhung loads and rotational bending)
د) بارهای پیچشی (Torsional loads)
ه) بارهای محوری (Axial loads)
الف) اضافه بار: هر شفت برای تحمل مقدار مجازی از تنش طراحی شده است و اگر تنش از حد مجاز تجاوز کند سبب تخریب آن خواهد شد. شکست در اثر اضافه بار هم میتواند شکلپذیر(Ductile) یا ترد (Brittle) باشد. شکست ترد معمولاً همراه با علائم شورون -وی شکل- (Chevron Marks)، است. این فلشها همیشه به جایی اشاره میکند که ترک شروع شده است. ظاهر یک شکست، چه شکلپذیر یا ترد، به عوامل مختلفی از جمله جنس شفت، نوع و بزرگی بار، و دمای شفت در هنگام خرابی بستگی دارد.
ب) بارهای چرخهای یا خستگی: در مورد بارهای چرخهای یا خستگی پیشتر صحبت شد هر چرخه بارگذاری و باربرداری نیرو سبب اعمال بارهای چرخهایی به شفت میشود.
ج) بارهای چرخشی خمشی: بارهای چرخشی خمشی مانند تنشی که یک پولی بزرگ بر روی شفت اعمال میکند و سبب اعمال خمش و چرخش تواماً میشود.
د) بارهای پیچشی: در اثر چرخش شفت به آن وارد میشود.
ه) بارهای محوری: بارهای محوری بیشتر بر روی بیرینگهای شفت (بلبرینگ و رولبرینگ) اعمال میشوند و سبب ایجاد تخریب رینگ داخلی آن میشوند.
۲) تنشهای محیطی
تنشهای محیطی (Environmental Stress)، مجموعه عواملی هستند که باعث خوردگی، سایش شفت میشوند و شامل زیر هستند: رطوبت (Moisture)، فرسایش (Erosion)، خوردگی (Corrosion) و کاویتاسیون (Cavitation).
الف) خرابی در اثر خوردگی (Corrosion Failures): هسته اصلی این مشکل یک واکنش الکتروشیمیایی است که سبب از بین رفتن قسمتی از فلز شفت و منجر به ایجاد حفره بر روی آن میشود. خوردگی میتواند خرابی در اثر خستگی را تسریع ببخشد و هم میتواند با از دست رفتن قسمتی از شفت باعث شکست شفت در بارگذاریهای کمتر شود.
ب) کاویتاسیون (Cavitation): در کاربردهای پمپاژ جریان مایع، که مایع متلاطم از روی شفت عبور میکند، پدیدهای به نام کاویتاسیون میتواند رخ دهد. پدیده کاویتاسیون سبب فرسایش سطح شفت میشود.
ج) فرتینگ (Shaft Fretting): پدیدهی فرتینگ میتواند آسیب جدی به شفت وارد کند. علت این پدیده حرکت بین دو قسمت مونتاژ شده (Mating Part) و وجود اکسیژن در هوا است. زمانی که قسمت مونتاژ شده به شفت مانند بلبرینگها، کوپلینگها و غیره دارای کمی لغزش باشند قسمتی از فلز سائیده میشود و در مجاورت در هوا اکسید میشوند. این ذرات اکسید به عنوان یک ساینده عمل میکنند و به سرعت سطح شفت را دچار سایش میکنند.
۳) تنشهای حرارتی
تنشهای حرارتی (Thermal Stresses)، هنگامی که یک موتور در حال کار است، معمولاً تحت تنش حرارتی قرار دارد. تنش حرارتی میتواند سبب بروز مشکلاتی مانند: اضافه بار، خرابی بلبرینگ و از دست دادن تلرانسها و انطباقات شود.
۴) تنشهای باقیمانده
تنشهای باقیمانده (Residual Stress)، تنش پسماند مستقل از بار خارجی روی شفت است. روشهای ساخت و تعمیر بسیاری وجود دارد که میتواند تنش پسماند را در شفت ایجاد کند که ممکن است خرابی را تسریع کند. عامل به وجود آوردن این تنشها توانند مکانیکی یا حرارتی باشند. برخی از آنها عبارتند از: ماشین کاری، عملیات حرارتی و شات پینینگ. تمام تنشهای پسماند برای شفت مضر نیستند. اگر تنش موازی با تنش بار و در جهت مخالف باشد، ممکن است مفید باشد.
۵) تنشهای الکترومغناطیسی
تنشهای الکترومغناطیسی (Electromagnetic Stress)، باعث بروز حداقل دو مسأله میشوند.
الف)
اعمال بار شعاعی بیش از حد (Excessive Radial Load) که ناشی از قرارگیری
شفت در وضعیت خارج از مرکز روتور به علت نیروهای الکترومغناطیس است
میتواند در صورت بلند بودن شفت نیروی زیاد شعاعی و خمشی به شفت وارد کند و
خرابی بیرینگهای شفت را تسریع ببخشد.
ب) بسته شدن خارج از فاز
(Out-of-phase Reclosing)، اعمال ولتاژ بیشتر از مقدار تعریف شده میتواند
مقدار زیادی گشتاور روی شفت ایجاد کند و مقدار زیاد گشتاور میتواند با
اعمال تنش پیچشی بیشتر سبب خرابی شفت شود.