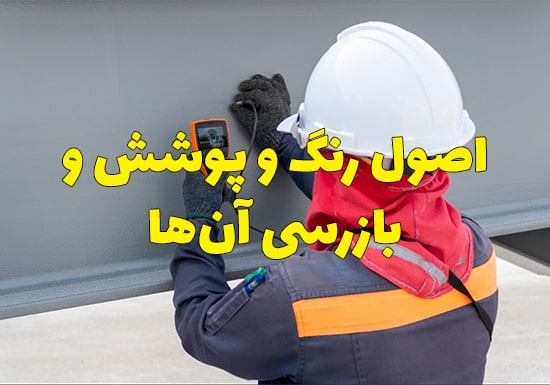
۰ تا ۱۰۰ اصول رنگ و پوشش و بازرسی آنها
کلمه پوشش
(Coating) در کنار کلمه رنگ (Painting) دو اصطلاح عمومی میباشند که ممکن
است به جای یکدیگر استفاده شوند. به طور کلی، پوشش محافظی در برابر خوردگی
است، در حالی که رنگ ممکن است دارای خواص اضافی مانند رنگدانههای محافظت
در برابر اشعه فرابنفش (Ultraviolet Screening Pigments) باشد.
اصطلاح
دیگری که اغلب با هم استفاده میشود لاینینگ (Lining) است که برای توصیف
پوشش سطوح داخلی لولهها یا مخازن استفاده میشود. در حالیکه برای شناسایی
پوشش سطوح خارجی همیشه از اصطلاحات رنگ یا پوشش استفاده میشود.
اثربخشی
یک پوشش به انتخاب مواد پوششی بستگی دارد که با کاربرد مورد نیاز مطابقت
داشته باشد. امروزه انتخاب پوشش بر اساس کاربرد مورد انتظار، نتایج عملکرد
پوشش و ارزیابی از مقدار مؤثر بودن پوشش میباشد. سازمانهایی که
استانداردهایی را برای تعیین مواد پوشش، آمادهسازی سطح، کاربرد، بازرسی و
آزمایش تعریف میکنند به شرح زیر است:
انجمن آزمایش و مواد آمریکا (ASTM) – American Society for Testing and Materials
انجمن ملی مهندسین خوردگی (NACE) – National Association of Corrosion Engineers
انجمن رنگ سازههای فولادی (SSPC) – Steel Structures Painting Council
در
مقاله «۰ تا ۱۰۰ اصول رنگ و پوشش و بازرسی آنها» به بررسی ترکیبات شمیایی
پوششها و رنگها پرداخته نخواهد شد و آنچه که در ادامه خدمت علاقهمندان
ارائه میشود به روشهای آمادهسازی سطح (Surface Preparation)، کاربرد
(Application) و بازرسی سطح (Inspection Methods) در بحث رنگ و پوشش
میباشد.
مفاهیم اولیه
خوردگی
(Corrosion): دلیل اصلی پوشش فولاد برای جلوگیری از خوردگی است. خوردگی
فلزات یک واکنش الکتروشیمیایی است که میتواند با حذف یک یا چند عنصر از
چهار عنصر مورد نیاز برای ایجاد خوردگی، آن را کنترل کرد. که این چهار عنصر
به شرح زیر میباشند.
۱) آند (Anode): دچار خوردگی میشود.
۲) کاتد (Cathode): دچار خوردگی نمیشود.
۳) الکترولیت (Electrolyte): به آب یا رطوبت در جو و… گفته میشود.
۴) مسیر فلزی (Metallic path): به تماس به دو فلز مختلف یا دو قمست یک فلز گفته میشود.
متداولترین انواع خوردگی که در فلزات آهنی با آن مواجه میشوند؛ به شرح زیر میباشد.
الف)
خوردگی یکنواخت (Uniform Corrosion): این خوردگی که کم و بیش به صورت
یکنواخت رخ میدهد و منجر به زنگ زدگی (Rust) و از بین رفتن فلز روی سطح
میشود.
ب) خوردگی گالوانیکی (Galvanic Corrosion): این نوع از خوردگی
زمانی اتفاق میافتند که دو فلز غیر هم جنس در یک الکترولیت (مثلاً آب) با
هم در تماس باشند. در نتیجه این بر هم کنش فلز فعالتر خورده میشود.
ج)
خوردگی شکافی (Crevice Corrosion): خوردگی شکافی شکلی از خوردگی موضعی
(Localized Corrosion) است که در شکاف و درزها یا سایر نقاطی که سطوح فلز
روی هم قرار گرفتهاند و سبب ایجاد گوشه شدهاند و در شرایطی که در معرض
مواد خوردنده قرار دارند، به وجود میآید. این نوع خوردگی معمولاً به علت
وجود مقادیری محلول که سبب ایجاد تعدادی واکنش زنجیرهایی میشود، به وجود
میآید. برای مثال در خوردگی شکافی فولاد در ابتدا فلز احیا میشود
(الکترون از دست میدهد) و فلز احیا شده با یون کلرو (یون منفی کلر) واکنش
میدهد و سبب تخلیه فلز میشود. این نوع خوردگی در بین اتصالات پرچ شده، اتصالات فلنجها و… به صورت گسترده دیده شده است.
د)
خوردگی حفرهای (Pitting Corrosion): خوردگی حفرهای شکلی از خوردگی موضعی
(Localized Corrosion) است که مکانیزم عملکرد آن بسیار شبیه به خوردگی
شکافی است. این خوردگی از خطرناکترین نوع خوردگیها میباشد چرا که تشخیص
آن به علت این که فقط نقاط کوچکی از فلز مورد حمله قرار میگیرد بسیار
دشوار است. این نوع خوردگی در مجاورت محلولهای حاوی آنیون خوردنده مخصوصاً
یون منفی کلر، معمولاً به وجود میآید.
ه) خوردگی سایشی (Erosion
Corrosion): اگر سطح یک جسم توسط حرکت یک سیال که حامل ذرات جامد و غیره
است دچار سایش شود، به آن پدیده سایشی گفته میشود. حال اگر سیال خورنده
باشد این اثر تشدید میشود که به آن خوردگی سایشی گفته میشود.
۱) آمادهسازی سطح
آمادهسازی سطح یا Surface Preparation، اولین اقدام در بحث رنگ و پوشش میباشد. خرابیهای زودرس اغلب نتیجه آمادهسازی ناکافی سطح است. وجود آلودگی زیر سطح سبب کاهش عمر پوشش میشوند. بنابراین، تمیزی سطح زیرین جزء ضروری و جدایی ناپذیر اصول رنگ و پوشش میباشند. انواع آلودگیهای سطحی عبارتند از: زنگ زدگی (Rust)، آلودگی روغن و گریس (Grease and Oil)، گرد و خاک (Dirt and Dust)، آب (Water)، پوشش خراب شده قبلی (Deteriorated Coatings) و…
۱-۱) استانداردهای آمادهسازی سطح
استانداردهای
متعددی جهت آمادهسازی سطح وجود دارد. بازرس باید اطمینان حاصل کند که
استاندارد مربوطه قابل اجرا در محل کار (Jobsite) است. آنچه که برای
استانداردهای بازرسی چشمی رنگ و پوشش میآید، مکمل اقدامات در جهت
آمادهسازی سطح میباشند. برای اطلاعات بیشتر از تفاوتهای کد و استاندارد
مقاله بررسی تفاوتهای استاندارد، کد و اسپسیفیکیشن را مطالعه کنید. برخی از این استانداردها به شرح زیر میباشند.
۱) استاندارد SSPC-SP1 به بررسی پاکسازی با محلول (Solvent Cleaning) میپردازد.
۲) استاندارد SSPC-SP2 به بررسی پاکسازی با ابزار آلات دستی (Hand Tool Cleaning) میپردازد.
۳) استاندارد SSPC-SP3 به بررسی پاکسازی با ابزار آلات قدرتی (Power Tool Cleaning) میپردازد.
۴)
استاندارد SSPC-SP5/NACE 1 به بررسی پاکسازی با ذرات ساینده (White Metal
Blast Cleaning) میپردازد. این استاندارد به بررسی استفاده از مواد ساینده
برای حذف آلودگی روغن و گریس، کثیفی گرد و غبار، زنگ زدگی، پوششها و سایر
مواد خارجی میپردازد.
۵) استاندارد SSPC-SP 8 به بررسی پاکسازی با حمام اسید (Pickling) میپردازد. از بین بردن زنگ زدگی با واکنش شیمیایی (حمام اسید) یا الکترولیز (جریان الکتریکی آندی) در این استاندارد بحث شده است.
۱-۲) تقسیمبندی روشهای آمادهسازی سطح
برای رسیدن به
پوشش مناسب، انجام آمادهسازی سطح درست حیاتی میباشد. این مرحله علاوه بر
اینکه از اهمیت بالایی برخوردار است، پرهزینهترین مرحله پوشش دهی میباشد.
طول عمر پوششها به میزان درجه آمادهسازی سطح بستگی فراوانی دارد. دو
دلیل اصلی برای آمادهسازی سطح وجود دارد.
۱) برای تمیز شدن سطح به منظور کاهش تخریب زود هنگام سیستمهای پوششی انجام میشود.
۲) برای به دست آوردن سطحی با زمینه و زبری مناسب که به راحتی توسط رنگ مرطوب شود تا چسبندگی رنگ به سطح را افزایش دهد.
به طور کلی روشهای آمادهسازی سطح به شکل زیر طبقهبندی میگردند.
۱) روشهای مکانیکی
روشهای مکانیکی، به روشهایی گفته میشود که رنگ و آلودگیها را به صورت مکانیکی از روی سطح بر داشته میشود.
۲) روشهای شیمیایی و فیزیکی
روشهای
شیمیایی، به روشهایی گفته میشود که رنگ و آلودگیها را به وسیله غوطه ور
شدن در محیط اسیدی یا قلیایی از بین برده میشود. همچنین در روشهای
فیزیکی، اعمال حرارت سبب پاکسازی سطح خواهد شد.
۱-۲-۱) تمیز کاری با ابزار دستی
تمیز کاری با ابزار دستی یا به انگلیسی Scrapping Hand Tool Cleaning، در دسترسترین روش برای آمادهسازی سطح است. این روش با استفاده از ابزارهایی مانند: کاردک، برس زبر، سمباده و وسایل ساینده زنگ و آلودگی انجام میشود. این روش زمان بر میباشد و تأثیرگذاری نسبتاً پائینی دارد.
۱-۲-۲) تمیز کاری با ابزار برقی
تمیز کاری با ابزار برقی یا به انگلیسی Impact Power Tool Cleaning، تمیز کاری با استفاده از برسهای سیمی که توسط یک دستگاه میچرخند انجام میشود.
۱-۲-۳) تمیز کاری به کمک سند بلاست
تمیز کاری به کمک سند بلاست یا به انگلیسی Impact Power Tool Cleaning، یک روش کارآمد و نسبتاً جدید است که با برخورد ذرات ساینده شن با سرعت بالا به سطح قطعه کار سبب زودن رنگ و سایر آلودگیها از روی سطح آن میشود.
۱-۲-۴) تمیز کاری به کمک شعله
تمیز کاری به کمک شعله یا به انگلیسی Flame Cleaning، جزء روشهای شیمیایی آمادهسازی سطح میباشد. در این روش اعمال حرارت بر روی سطح سبب سوختن رنگ میشود و سپس با کمک برس سیمی و در صورت لزوم یک حلال سطح پاکسازی میشود.
۱-۳) معیار ارزیابی آمادهسازی سطح
برای
ارزیابی میزان آمادهسازی سطح، استانداردهای ISO، SSPC و NACE/SSPC
تصاویری را جهت راهنمایی ارائه کردهاند. این تصاویر صرفاً جهت راهنمایی
دارد و نباید منجر به تغییر گفته شده در استانداردهای آمادهسازی سطح شود.
علت این موضوع این است که انجام یک عملیات آمادهسازی سطح برای دو سطح
مختلف فولادی ممکن است به لحاظ ظاهری نتیجه متفاوتی را داشته باشد.
استاندارد
ISO 8501، یک استاندارد تصویری است که نمایانگر درجههای مختلف زنگ زدگی
در سطوح مختلف تمیزی است، همچنین حاوی توضیحات متنی سطوح تمیزی است.
استاندارد ملی چین GB 8923-88 که توسط مؤسسه استاندارد ملی چین ارائه شده
است درجه آمادهسازی با سند بلاست به چهار گروه تقسیمبندی میکند که که با
حرف “Sa” نشان داده میشود.
سند بلاست Sa 1: سند بلاست Sa 1، سند بلاست آرام (Mild Spray) است که هیچ چربی یا کثیفی قابل رؤیت روی سطح فولاد وجود ندارد.
سند
بلاست Sa 2: سند بلاست Sa 2، سند بلاست کامل (Thoroughly Spray) است که
روی سطح فولادی نباید هیچ گونه گریس، کثیفی، رسوب اکسید، زنگ زدگی و سایر
ملحقات قابل مشاهده وجود داشته باشد رنگ باقی مانده باید به صورت خاکستری
دیده شود.
سند بلاست Sa 2.5: سند بلاست Sa 2.5، سند بلاست بسیارکامل
(Very Thorough Spray) است که هیچ گونه چربی، کثیفی، رسوب اکسید، زنگ زدگی،
پوشش رنگ و سایر ملحقات روی سطح فولاد نباید قابل مشاهده باشد و هر اثر
باقی مانده باید فقط لکهها یا نوارهای روشن باشد.
سند بلاست Sa 3: سند بلاست Sa 3، سند بلاست کامل است که پس از آن درخشندگی فلز قابل رؤیت میباشد.
۲) کاربردها و شرایط پوشش
کاربردها و شرایط پوشش یا Coating Applications and Conditions، به بررسی انواع پوششها و کاربردشان و همچنین روشهای اعمال آنها میپردازد.
۲-۱) آشنایی با اجزای سازنده پوشش
پوشش یا Coating از سه بخش زیر تشکیل شده است.
۱) حلال (Solvent)
۲) رزین (Resin)
۳) رنگدانه (Pigments)
پوششها
میتوانند حلال و اجزای رنگدانهای نداشته باشند. به عنوان مثال پوششهای
بدون حلال (با ۱۰۰ درصد مواد جامد) و بدون رنگدانه وجود دارد، اما پوششهای
بدون رزین وجود ندارد.
۲-۱-۱) حلال
فرمولهای شیمیایی اجزای حلال، رزین و رنگدانه معمولاً به دو دسته کلی تقسیم میشوند:
الف)
دسته اول: حلال و رزین را با هم ترکیب میکند. بخش حلال، قسمت فرار
(Volatile Vehicle) و بخش رزین، قسمت غیرفرار (Nonvolatile Vehicle)
میباشد.
ب) دسته دوم: رنگدانه است. رنگدانهها افزودنیهایی هستند که
خواص خاصی به پوشش میدهند و به دو دسته کلی تقسیم میشوند: رنگی، تقویت
شده بیاثر. هنگامی که یک پوشش اعمال میشود، حلال در طول فرآیند پخت تبخیر
میشود و تنها رزین و اجزای رنگدانه بر روی بستر باقی میماند که گاهی
اوقات پوشش جامد (Coating Solids) نامیده میشود و لایه محافظ برای محافظت
در برابر خوردگی را تشکیل میدهند.
اصطلاحات حلال (Solvents) و رقیقکننده (Thinners) اغلب به جای یکدیگر استفاده میشوند. در برگه اطلاعات سازنده معمولاً نوع رقیقکننده مورد استفاده را مشخص میکند. استفاده از رقیقکنندههایی که توسط سازنده توصیه نمیشود میتواند باعث ایجاد مشکل یا خرابیهای زودهنگام مانند جدا شدن پوشش، انعقاد، خشک شدن خیلی سریع یا خیلی آهسته و…. شود.
۲-۱-۲) رزین
رزین (Resin)
یا بایندر (Binder) که جزء اصلی تشکیل دهنده پوشش است، معمولاً از یک پلیمر
جامد با وزن مولکولی بالا که مولکولهای تکرار شونده دارد تشکیل شده است.
هدف اصلی رزین خیس کردن ذرات رنگدانه و اتصال ذرات رنگدانه به یکدیگر و به
بستر است.
انواع رزینها با توجه به شرایط زیر فرموله و ساخته میشوند.
عملکرد در نوع قرار گرفتن در معرض خدمات
عملکرد بر روی نوع بستر
سازگاری با سایر پوششها
چسبندگی
۲-۱-۳) رنگدانه
رنگدانهها (Pigments) افزودنیهای شیمیایی به فرمول پوشش هستند که خواص خاصی را به آن میدهند. این خواص به صورت زیر میباشند.
رنگ
(Color): رنگدانهها میتواند طبیعی یا مصنوعی باشند. رنگدانهها طبیعی
زمین (رس کائولن، سیلیکات منیزیم، کربنات کلسیم) ثبات رنگ را در برابر زوال
اشعه ماوراء بنفش (UV) خورشید فراهم میکنند.
کدر بودن (Opacity): اکسید تیتانیوم زیرلایه یا رنگ پوشش قبلی را پنهان میکند و از رزین در برابر خرابی مقابل اشعه UV خورشید محافظت میکند.
رنگ مرطوب (Wet Paint): سیلیس و تالک ویسکوزیته را کنترل میکنند، سطح لایه مرطوب و ته نشین شدن را کنترل میکنند، اما قدرت پنهانسازی (کدری) کمی دارند.
مقاومت در برابر رطوبت (Weather and Moisture Resistance): ورقههای آلومینیوم و اکسید آهن میکایی Micaceous Iron Oxide (MIO) برای ساخت پوششهای رنگ استفاده میشود. این مواد مانع با دفع رطوبت باعث کاهش خوردگی میشوند.
مقاومت در برابر خوردگی (Corrosion Resistance): رنگدانههای اضافه شده به پوششهای زیرین (Primer) مانع از خوردگی آهن میشوند. بسترها فرمولاسیونهای گذشته شامل رنگدانههای کرومات و سرب بود، اما امروزه به ندرت به دلیل نگرانیهای زیست محیطی و بهداشتی مورد استفاده قرار میگیرند و با مواد جدیدتر جایگزین شدهاند.
۲-۲) روشهای اعمال پوششها
در این قسمت به روشهای اعمال پوششها یا Coatings Application Methods میپردازیم. پوششها یا تک جزئی (Single Component) یا چند جزئی (Multiple Component) هستند. قبل از اعمال، مواد پوشش نیاز به مخلوط کردن دارند تا رنگ یکدست و یکنواخت شود. مایعات و رنگدانهها با چگالیهای مختلف ممکن است از هم جدا شوند، ته نشین شوند. پوششهای چند جزئی مانند اپوکسیها، که حاوی رزین و سختکننده هستند و میتوانند به نسبت مساوی یا نابرابر باشند که بر اساس حجم تعیین میشود. اجزاء باید در بستهبندیهای جداگانه، برای مخلوط کردن حمل شوند. در زیر شرح کاربرد، تجهیزات و روشهای اعمال پوششها آورده شده است.
۱) قلم مو (Brush): قلم مو معمولاً برای مناطق کوچک، نواحی تعمیر و شکافها استفاده میشوند. قلم موها در اندازهها، شکلها مختلف هستند.
۲)
غلتکها (Rollers): غلتکها که از نظر قطر، طول، نوع پارچه و طول الیاف
متفاوت هستند و معمولاً برای مناطق مسطح بزرگ (سطوح افقی و عمودی) استفاده
میشوند.
۳) اسپری (Spray): اسپری میتواند در دو نوع زیر باشد:
الف)
اسپری معمولی (Conventional Spray): دارای تجهیزات ساده و ارزان میباشد و
به طور وسیعی مقبولیت داشته و مورد استفاده قرار میگیرد. در این روش ذرات
رنگ توسط جریان هوا پر فشار بر روی سطح قطعه کار پاشیده میشود. جریان هوا
پر فشار توسط کمپرسور ایجاد میشود.
ب) اسپری بدون هوا (Airless Spray): در این روش سیال (رنگ) توسط پمپ تحت فشار قرار میگیرد. در این روش پمپهای موتور الکتریکی و پمپهای هیدرولیک
نیز مورد استفاده قرار میگیرند، اما رایجترین آنها پمپهایی است که با
هوای فشرده کار میکنند. رنگ با کمک فشار اعمال شده و عبور از نازلهای
خروجی به شکل پودر در میآید و بر روی سطح پاشیده میشود. مزیت این روش
نسبت به اسپری معمولی به صورت زیر است. ۱) سرعت بالای رنگآمیزی ۲) اجرای
رنگ با ضخامت زیاد ۳) کاهش ضایعات
۴) رنگ الکترواستاتیک (Electrostatic Spray):
رنگ الکترواستاتیک یک فرایند رنگآمیزی است که در آن از اصول الکترواستاتیک برای تهیه و اعمال رنگ استفاده میشود. این روش معمولاً برای رنگآمیزی اجسام فلزی مورد استفاده قرار میگیرد. فرآیند رنگ الکترواستاتیک به این صورت است که قطعات فلزی با استفاده از یک تابش یونیزهکننده الکترواستاتیک باردار میشوند. این تابش، بارهای الکتریکی مثبت را بر روی قطعه فلزی ایجاد میکند و در عین حال بارهای الکتریکی منفی را بر روی پودر رنگ ایجاد میکنند. در نهایت با استفاده از برقراری شارژهای الکتریکی رنگ به سطح قطعه جذب میشود و به طور یکنواخت روی سطح توزیع میشود.
۳) بازرسی رنگ و پوشش
بازرسی
رنگ و پوشش یا Coating & Painting Inspections، توسط بازرس مربوطه
انجام میشود. وظیفه بازرس مربوطه این است که بررسی کند آیا کیفیت کار
انجام شده مطابق با مشخصات و مطابقت با تمام اسناد قراردادی پروژه است یا
خیر. به معنای دقیق، قضاوت کار باید فقط بر اساس مستندات باشد.
بازرس
رنگ و پوشش برای انجام صحیح وظایف، باید دستگاه بازرسی مناسب کار را داشته
باشد که انواع مختلفی دارد، اما لیست زیر باید برای اکثر پروژهها کافی
باشد.
۱) دما و رطوبت سنج (Electronic Relative Humidity Temperature Meter)
۲) ضخامت سنج فیلم خشک (Dry Film Thickness Gauge)
۳) چراغ قوه (Flashlight)
۴) بازرسی آینه یا بوروسکوپ (Inspection Mirror or Boroscope)
۵) ذره بین یا میکروسکوپ دیجیتال (Magnifying Glass or Digital Microscope)
۶) تجهیزات تست نمک (رسانایی یا کلرید) (Salt Testing Equipment (Conductivity or Chlorides))
۳-۱) عیوب رنگ و پوشش
در ادامه برخی از شایعترین عیوب رنگ و پوشش را بررسی میکنیم. تصاویر عیوب رنگ و پوشش، در ادامه مقاله آورده شده است.
۳-۱-۱) خونریزی (Bleeding)
خونریزی یا Bleeding به لکه دار شدن پوشش بالایی گفته میشود. علت به وجود آمدن این عیب، مهاجرت رزینها یا رنگدانههای محلول در لایه زیرین به لایه رویی میباشد. برای جلوگیری از این مشکل، از مواد رنگی با مقاومت حلال کافی استفاده شود.
۳-۱-۲) تاول (Blistering)
تاول یا Blistering، به حبابهای نیمکرهای کوچک تا بزرگ در پوشش که حاوی گازها یا مایعات است، گفته میشود. علت به وجود آمدن این عیب، ممکن است به دلیل آمادهسازی ضعیف سطح، مواد محلول داخلی یا خیس بودن سطح باشد. برای جلوگیری از این مشکل، پوششی با قدرت چسبندگی بسیار قوی انتخاب کنید و از تمیزی سطح با آمادهسازی سطح مناسب مطمئن شوید.
۳-۱-۳) بتن (Concrete)
بتن یا Concrete، نوعی عیب در پوشش است که سبب از بین رفتن چسبندگی یا پوسته شدن پوشش میشود. علت به وجود آمدن این عیب، ممکن است واکنش شیمیایی، تشکیل نمکهای کلسیم در زیر پوشش و رطوبت بالا باشد. برای جلوگیری از این مشکل، سطح با شدت زیاد سند بلاست آمادهسازی شود و از یک لایه زیرین با نفوذ بالا و وزن مولکولی کم استفاده شود.
۳-۱-۴) ترک خوردگی (Cracking)
ترک خوردگی یا Cracking، به وجود ناپیوستگی ترک در پوشش گفته میشود. علت به وجود آمدن این عیب، ممکن است به دلیل اکسیداسیون مداوم و استفاده از رنگدانه نامناسب یا سیستم پوشش نامناسب باشد. برای جلوگیری از این مشکل، از رزینهای خنثی و مقاوم در برابر شرایط محیطی استفاده شود و رنگدانههای تقویت شده و خنثی با لایه رنگ زیرین استفاده شود.
۳-۱-۵) قلل و فرج (Cratering)
قلل و فرج یا Cratering، به وجود فرورفتگیهای کوچک و یکنواخت در پوشش گفته میشود. علت به وجود آمدن آن حبس حبابهای هوا در فیلم مرطوب حین اسپری رنگ میباشد. برای جلوگیری از این مشکل، با سندبلاست از حذف آلایندهها در ناهمواریها اطمینان حاصل کنید.
۳-۱-۶) پوست پرتقالی (Orange Peel)
پوست پرتقالی یا Orange Peel، به ایجاد ظاهر کلی ناهموار در پوشش گفته میشود که شبیه پوست پرتقال است. علت به وجود آمدن آن سطح فیلم صاف اما نامنظم است که ناشی از به کارگیری تکنیکهای نامناسب مانند: قرارگیری نازل خیلی دور از سطح، تبخیر سریع حلال، فشار کم اسپری برای اتمیزه شدن و رنگ خیلی چسبناک است. برای جلوگیری از این مشکل، سعی در برطرف کردن علتهای نام برده شده کنید.